3D Printing Hair Accessories: Complete Tutorial Guide 2025
We've all been there – searching endlessly for the perfect hair accessory that matches our style, fits our hair type, and won't break after a few uses. Traditional store-bought clips and combs often disappoint with their generic designs and poor durability. But what if we told you there's a revolutionary way to create exactly what you need?
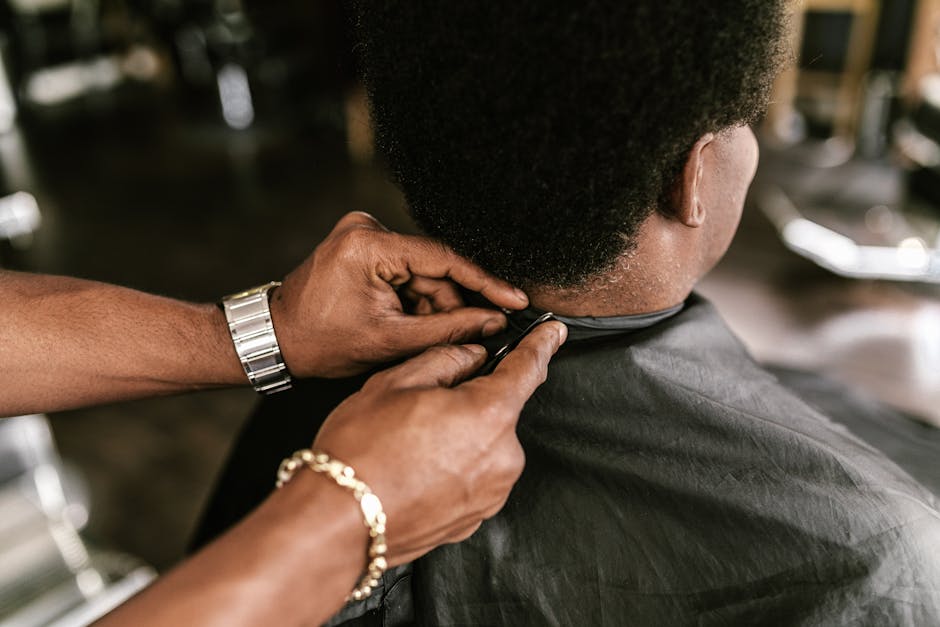
We've all been there – searching endlessly for the perfect hair accessory that matches our style, fits our hair type, and won't break after a few uses. Traditional store-bought clips and combs often disappoint with their generic designs and poor durability. But what if we told you there's a revolutionary way to create exactly what you need?
Affiliate disclosure: As an Amazon Associate, we earn from qualifying purchases.
Welcome to the exciting world of 3D printed hair accessories! This comprehensive guide will walk you through every step of creating custom, durable, and beautiful hair accessories from the comfort of your home. Whether you're a complete beginner or looking to refine your techniques, we'll help you master this rewarding craft that combines technology with personal style.
Getting Started: Essential Equipment and Software
Choosing the right 3D printer for hair accessories doesn't require breaking the bank. We recommend starting with a reliable FDM printer that offers precision and consistency. The Creality Ender 3 V2 3D Printer provides excellent value with its 220x220x250mm build volume – perfect for most hair accessory projects.
For software, beginners should start with Tinkercad (free, browser-based) or Fusion 360 (free for personal use). These platforms offer intuitive interfaces for creating basic shapes and modifications. Advanced users might prefer Blender for organic designs or SolidWorks for precise engineering.
Essential post-processing tools include the REPTOR 3D Printer Tools Kit with scrapers, nozzle cleaning tools, and precision knives. Don't forget safety equipment: safety glasses, dust masks for sanding, and well-ventilated workspace are non-negotiable.
Budget approximately $200-400 for a complete starter setup including printer, filament, and tools. This investment pays for itself quickly when you consider the cost of quality store-bought accessories over time.
Material Selection: PLA vs PETG for Hair Accessories
Material choice significantly impacts your accessory's durability, comfort, and safety. PLA (Polylactic Acid) offers excellent printability and eco-friendliness, making it perfect for beginners. It's biodegradable, derived from corn starch, and prints at lower temperatures (190-220°C), reducing warping issues.
However, PLA has limitations. It becomes soft around 60°C, making it unsuitable for hot styling tools or sunny car dashboards. For hair accessories requiring flexibility, like headbands or scrunchie holders, PLA might crack under repeated stress.
PETG (Polyethylene Terephthalate Glycol) provides superior durability and flexibility. It withstands higher temperatures (80°C+) and offers excellent impact resistance. The SUNLU PLA+ Filament combines PLA's ease of printing with enhanced strength properties.
For color variety, both materials offer extensive options. Consider skin-safe certifications when selecting filaments, especially for accessories touching sensitive scalp areas. Always verify your chosen filament meets food-grade standards as an additional safety measure.
Design Principles for Hair-Safe Accessories
Creating hair-safe accessories requires understanding both form and function. Sharp edges or rough surfaces can damage hair cuticles or cause scalp irritation. We always design with rounded edges and smooth transitions between surfaces.
Consider hair type when designing. Fine hair requires lighter accessories with gentler gripping mechanisms, while thick, coarse hair needs stronger, more robust designs. Curly hair benefits from wider-toothed combs and larger surface areas for clips to distribute pressure evenly.
Structural integrity depends on proper wall thickness and infill patterns. Hair clips need 2-3mm walls for durability, while decorative elements can use 1-2mm. Use 20-30% infill for functional parts and 10-15% for purely decorative elements to balance strength with material efficiency.
Always research existing patents before selling designs. The USPTO database and Google Patents provide free searches. Focus on creating original interpretations rather than copying existing products. Document your design process to establish creation dates if needed.
Multi-Color Printing Techniques
Creating stunning multi-color hair accessories doesn't require expensive multi-extruder printers. The pause-and-swap method works excellently for beginners. Simply pause the print at specific layer heights and manually change filament colors.
Plan color changes during the slicing process using software like PrusaSlicer or Cura. Mark layer heights where colors should change and prepare filament pieces in advance. This technique works best for distinct color zones rather than gradual transitions.
For more advanced techniques, consider the filament welding method where you physically join different colored filaments. This creates smooth transitions but requires practice to master the timing and temperature settings.
Post-processing painting offers unlimited color possibilities. Use the Apple Barrel Acrylic Paint Set for vibrant, durable colors. Always prime PLA surfaces first and seal with appropriate topcoats for longevity.
Troubleshooting Common Printing Issues
Warping represents the most common challenge when printing hair accessories. Thin, elongated shapes like combs and picks are particularly susceptible. Combat warping by using heated beds (60°C for PLA, 80°C for PETG) and ensuring proper first-layer adhesion.
Bed adhesion issues often stem from improper leveling or contaminated surfaces. Clean your print bed with isopropyl alcohol before each print and recalibrate regularly. Glass beds provide excellent flatness but may require adhesion aids like painter's tape or specialized sprays.
Layer adhesion problems manifest as weak, easily separated layers. Increase extruder temperature by 5-10°C increments and reduce printing speed to 40-50mm/s for better layer bonding. Insufficient cooling can also cause poor adhesion, so ensure part cooling fans operate correctly.
Support structure optimization prevents failed prints on complex shapes. Use tree supports for organic curves and linear supports for geometric overhangs. Set support density to 10-15% and enable support interface layers for cleaner removal.
Post-Processing for Professional Results
Professional-quality hair accessories require meticulous post-processing. Start with support removal using flush cutters and needle-nose pliers. Work slowly to avoid damaging the main structure, especially around delicate details.
Sanding creates smooth, comfortable surfaces essential for hair contact. Begin with 220-grit sandpaper for major imperfections, progressing through 400, 800, and 1200-grit for mirror-like finishes. The Sandpaper Variety Pack provides all necessary grits in convenient sheets.
Chemical smoothing using acetone vapor works excellently for ABS but isn't suitable for PLA or PETG. Instead, use specialized PLA smoothing solutions or stick to mechanical methods for these materials.
For functional elements like springs or hinges, precise drilling may be necessary. Use the Neiko Digital Caliper for accurate measurements and mark drill points carefully. Start with pilot holes and gradually increase bit sizes to prevent cracking.
Testing and Safety Considerations
Safety testing ensures your accessories won't cause harm during use. Perform stress tests by applying gradual force until failure occurs. Document breaking points and redesign if strength proves insufficient for intended use.
Skin sensitivity testing involves wearing new accessories for short periods initially. Watch for redness, itching, or irritation that might indicate material allergies. Some individuals react to certain plastics, making material selection crucial.
Hair damage prevention requires smooth surfaces and appropriate pressure distribution. Rough textures can catch and break hair strands, while excessive pressure points cause breakage and discomfort. Test accessories on various hair types when possible.
Cleaning protocols maintain hygiene and material integrity. Most printed accessories tolerate mild soap and water cleaning. Avoid harsh chemicals that might degrade plastic properties or cause color fading. Replace accessories showing wear, cracks, or surface degradation immediately.
Frequently Asked Questions
What's the best 3D printer for making hair accessories at home?
The Creality Ender 3 V2 offers excellent value with reliable performance, adequate build volume, and strong community support for beginners.
How long do 3D printed hair clips typically last with regular use?
Well-designed PETG accessories last 6-12 months with daily use, while PLA versions typically last 3-6 months depending on stress levels.
Can I sell 3D printed hair accessories legally without patent issues?
Yes, if you create original designs. Always research existing patents and avoid copying commercial products to prevent legal complications.
What post-processing steps are essential for skin-safe hair accessories?
Thorough sanding to remove layer lines, careful support removal, and stress testing ensure comfort and safety for skin contact.
How do I prevent my 3D printed hair picks from warping during printing?
Use heated beds, ensure proper first-layer adhesion, reduce printing speed, and consider adding brims or rafts for better bed adhesion.
Creating custom 3D printed hair accessories opens up endless possibilities for personal expression while solving practical styling challenges. We've covered everything from equipment selection to professional finishing techniques, giving you the foundation to create stunning, durable accessories that perfectly match your unique style.
Start with simple designs like basic clips or combs to build confidence and skills. As you master the fundamentals, gradually tackle more complex projects like articulated barrettes or multi-component headbands. Join online communities like Reddit's r/3Dprinting or Facebook groups dedicated to 3D printed accessories for inspiration, troubleshooting help, and design sharing opportunities.
Recommended Products
- Creality Ender 3 V2 3D Printer – Reliable, affordable printer perfect for hair accessory projects with excellent community support.
- SUNLU PLA+ Filament Multi-Color Pack – Enhanced strength PLA with vibrant colors ideal for durable hair accessories.
- REPTOR 3D Printer Tools Kit – Essential tools for print removal, cleaning, and maintenance with precision instruments.
- Neiko Digital Caliper – Precise measurements for design accuracy and quality control during post-processing.
- Sandpaper Variety Pack – Complete grit range for achieving professional smooth finishes on printed accessories.